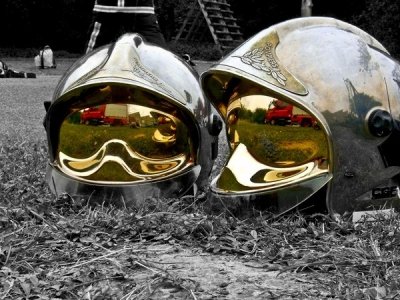
The Maine-et-Loire fire department deploys AWO to all sites
"In order to harmonize assistance and services to all people in the same county, state legislation brought about the creation of the SDIS (fire departments) organizations in the early 2000s. Our organizations went through a major shake-up. We went from municipal- to department-managed" says Commander Nicolas Thivent, Chief of the maintenance of logistics group at fire department 49 (Maine and Loire). «. Internally, it took almost 10 years to put all functional groups into place. The final modifications in the organization came around 2010 and since then our focus is to improve continuously." At fire department 49, the technical support to firefighters is handled by a centralized logistics support group. 30 people strong, it forms the logistical bridge between 80 barracks of the department and their suppliers. These vary from general stores and specialist workshops (clothing, small equipment, infrastructural- and mechanical assets). The centralized logistics support group manages purchases and maintenance for an asset base of 80 buildings, 700 rolling equipment, protective garments of 2,800 individual firefighters and 5,000 references to further gear: extinguishers, hoses, ladders etc.<br>
<br>
"In 2015, as part of our continuous improvement, we decided to simplify and standardize procedures handling requests for all barracks," continues the Commander Thivent. "First goal: allow the firefighters to focus on their primary duties. Second goal: improve the traceability of our procedures, to meet our regulatory obligations in a better and easier way, and by this we mean obligations concerning vehicles, protective garments, lifting equipment, fire extinguishers, etc. ".<br>
<br>
AS TECH Web Office chosen for its scalability and the company’s service excellence<br>
<br>
Following a public tender, tests were held to decide between the two companies who best responded to the specifications. SDIS 49 finally decided for AS-TECH Web Office (AWO) in October 2015. "We were attracted by the flexibility of the architecture and the integration of all features in a single, shared database for the dynamic management of stock," says lt. Denis Chauveau, deputy to commander Thivent, manager of Rolling equipment and AWO project leader. "Two other elements have also been crucial: AS-TECH Solutions’ politic to involve all its customers and users with the evolution of the software and their expertise in supporting long-term projects, like ours."<br>
<br>
Started in November 2015, currently, SDIS 49 is midstream. The data of the old obsolete solutions used by previously separated services have been integrated. General stores of small equipment are operational, as well as the management of protective clothing, 700 rolling gear, and infrastructure. And since 3 months, 16 barracks drivers are testing the one-stop computerized request. The goal for the year 2017: computerize all barrack requests.<br>
<h5>Targets achieved in record time thanks to the project team</h5>
<br>
"Looking at the amount of work that this all represents and given that officers involved had to conduct their daily tasks at the same time, we have achieved our goals in record time," continues commander Thivent. Key to this success? "Internally, the project leader and his first officer, lieutenant Chauveau and Marie-Laure Batilliot, both were dynamic and involved; from AS-TECH Solutions’ side, a single consultant was dedicated to the project. He helped us combining his excellent technical and relational skills. And finally, continuous communication to reduce the inevitable resistance to change to a minimum »<br>
<br>
Another key to success: "the ability to arbitrate, by better analyzing the needs to know when to adapt the solution to the procedures in place, or on the contrary, when enjoying the opportunity of good practices promoted by AS-TECH Web Office to adopt," says Marie-Laure Batilliot, Assistant manager of the rolling equipment department and administrator of the AWO solution. "The knowledge and experience of how a fire department functions of AS-TECH’s consultant have been very productive."<br>
<h5>Protective clothing, savings, and respect for the environment</h5>
<br>
Amongst the changes brought on by the solution was that paper purchase orders have been replaced by unified and dematerialized procedures. These allow traceability of spending, make a better analysis of cost and create indicators to make predictions. This way public spending is and better controlled and justifiable.<br>
<br>
Concerning clothing, the 2,800 firefighters previously had a flat budget to spend on an online catalog on the Intranet. Before the introduction of the AWO module, a change was decided: replace worn items (uniform, helmet, boots...), in function with the missions on which they had been used, without spending cap. A long time reform-wish, but which wasn’t supported by the old software. "In fact, this new practice translates into a reduction in the cost of the renewals”, says Lt. Chauveau. "With a constant budget, we can thus prospect for new equipment and gain further efficiencies. The clothing module ensures traceability of protective clothing and is also used for recycling purposes: some fibers and materials are reclaimed by partner companies for the manufacture of insulation of engine covers. »<br>
<h5>Alerts and dashboards to anticipate and make better decisions</h5>
<br>
SDIS 49 can set up alerts with AWO to make sure it adheres to regulatory obligations concerning protective gear, lifting tools, fire extinguishers, etc. This way regular checks will be performed. "These alerts avoid us particularly tedious tasks that mobilized a lot of energy," says Marie-Laure Batilliot. " and with the rolling equipment, AWO dashboards allow to follow more objective criteria to renew and/or repair”, adds Lieutenant Chauveau" Indeed, some barracks have new equipment, and their old equipment can be used to replace will replace older gear in other barracks based on AWO indicators (category, age, km, etc.). Our new solution helps us better to make these type decisions in a very short time. »<br>
<br>
Finally, this 3-month experience of 16 barracks, the request portal already shows its use in terms of traceability. This single point of entry for all requests automatically directs applicants (3 officers in each barracks) to the right catalog, then allows him to track the status of its application. The term goal is to win in terms of reactivity.<br>
<br>
Commander Thivent concludes: "these encouraging results tell us we have made the right choice in selecting AS-TECH Solutions!"<br>